علل خوردگی میلگرد
یکی از مهمترین عوامل تخریب سازههای بتن آرمه به ویژه در مناطق مرطوب خوردگی میلگرد میباشد. خوردگی میلگرد سبب بروز ترک در پوشش بتنی میلگرد شده و در نهایت تخریب سازه بتنی را به همراه دارد.
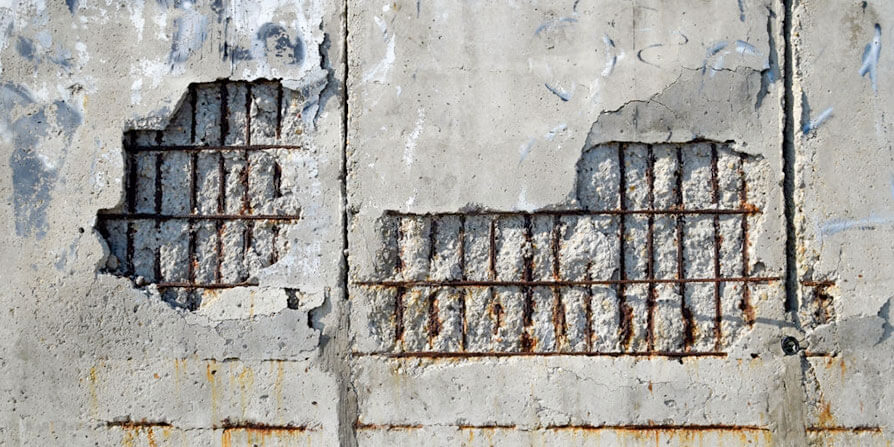
خوردگی یکی از علل اصلی پایداری محدود بتن مسلح شده با استفاده از میلگرد فولادی میباشد. محصول خوردگی که همان آهن زنگ زده است در مرز بین میلگرد فولادی و بتن باقی میماند. بنابرین باعث تخریب پیوند بین بتن و میلگرد فولادی میشود. مهمترین عامل خوردگی بتن نفوذ یون کلرید آزاد میباشد.
یونهای کلرید در بتن به سه حالت ذیل یافت میشوند:
- پیوند شیمیایی: مهمترین عامل موجود در بتن که سبب غیرفعال شدن کلرید آزاد میشود ترکیب C3A میباشد، این ترکیب با کلرید ژیوند شیمیایی برقرار کرده و سبب تشکیل کلرور آلومینات کلسیم (C3A.CaCl2.10H2O) شده و بدین ترتیب یونهای کلرید غیرفعال میشوند. به همین دلیل استفاده از سیمان پرتلند نوع ۵ و یا سیمان های ضدسولفات که دارای C3A کمتری میباشند در بتن مسلح توصیه نمیشود.
- پیوند فیزیکی: یونهای کلرید با محصولات هیدراتاسیون موجود در ساختار بتن پیوند فیزیکی برقرار کرده و غیرفعال میشوند.
- یونهای کلرید آزاد: که مهمترین عامل خوردگی میباشند.
از طرفی دیگر میلگردها در داخل بتن به صورت فیزیکی و شیمیایی محافظت میشوند که در زیر به شرح آنها خواهیم پرداخت.
محافظت فیزیکی: همان پوشش بتن بر روی میلگرد میباشد که نفوذ عوامل خوردگی نظیر کلرید آزاد و دی اکسید کربن را به تأخیر میاندازد.
محافظت شیمیایی: در شرایط قلیایی سیمانِ تازه به دلیل وجود هیدروکسید کلسیم و قلیاییهای سدیم و پتاسیم یک لایه اکسیدی محافظ بر روی میلگرد فولادی تشکیل میشود و از خوردگی آن جلوگیری میکند.
شرایط خوردگی میلگرد
همانطور که در بالا نیز اشاره شد میلگرد فولادی در داخل بتن به صورت فیزیکی و شیمیایی محافظت میشود، اما زمانی که در شرایط شیمیایی مهاجم از قبیل کربناته شدن و یا حضور یون کلرید قرار میگیرند، Ph محیط کاهش یافته و سبب ایجاد پیل الکتروشیمیایی میشود. خوردگی در فولاد یک پدیده الکتروشیمیایی میباشد که در اثر تشکیل پیلهای الکتروشیمیایی آند و کاتد اتفاق میافتد.
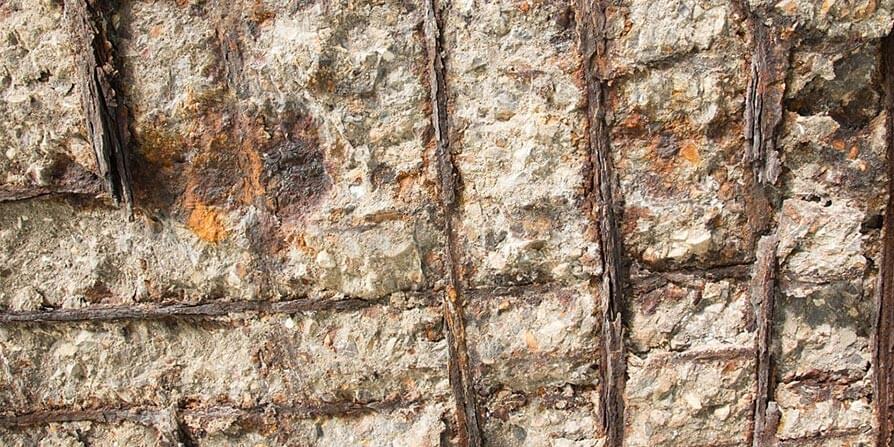
بخوانید:
روش های تقویت میلگرد برای محافظت در برابر خوردگی
خوردگی میلگرد و تکنیک های اندازه گیری آن
پدیده خوردگی میلگرد فولادی
زمانی که میلگرد فولادی تحت شرایط اختلاف پتانسیل الکتریکی قرار بگیرد، پیل الکتروشیمیایی دارای مناطق آندی و کاتدی که آب موجود در بتن الکترولیت آن را تشکیل میدهد، به وجود میآید.
واکنشهای کاتدی و آندی در پیل شیمیایی مذکور به شرح ذیل میباشند:
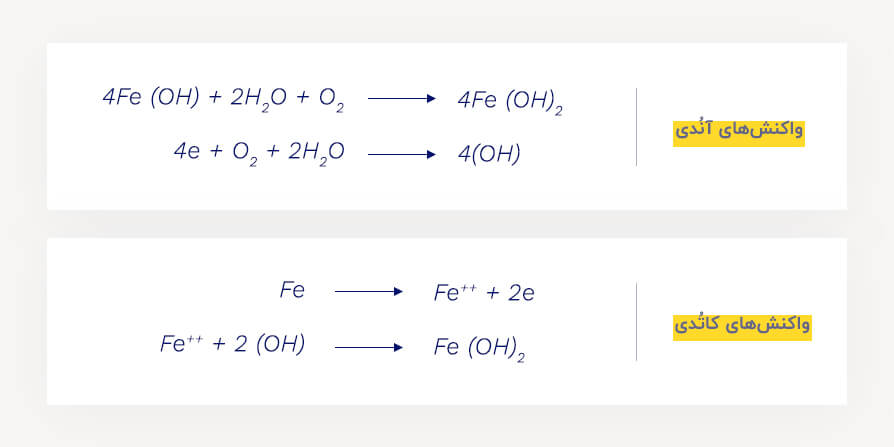
یون آهن با شار دو بار مثبت در آند وارد محلول شده و الکترون آزاد با شار منفی وارد کاتد میشود و در آنجا وارد الکترولیت شده، با آب و اکسیژن ترکیب و یونهای هیدروکسید را تشکیل میدهند.
یونهای هیدروکسید وارد الکترولیت شده و با یونهای آهن واکنش میدهند و در نتیجه هیدروکسید آهن را تشکیل میدهند که با اکسیداسیون بعدی به زنگ آهن تبدیل میشوند.
همانطور که در واکنشهای آندی و کاتدی مشاهده میشود، اکسیژن مصرف شده و آب تولید میشود و این واکنش جهت پایداری بتن ضروری است. بنابرین کنترل رطوبت موجود در بتن از مسائل ضروری میباشد. طبق تحقیقات بدست آمده میزان رطوبت استاندارد حدود ۶۰ درصد وزنی میباشد.
جهت تشریح تأثیر خوردگی بر قدرت پیوند بین فولاد و بتن بررسی سیستماتیکی از قدرت پیوند و مقاومت الکتریکی تماسی به عنوان تابعی از مدت زمان خوردگی بتن مسلح شده با استفاده از میلگرد فولادی انجام شده است. مقاومت الکتریکی تماسی کمیتی میباشد که با افزایش فاز بینابینی (فاز زنگ زده) به صورت یکنواخت افزایش مییابد. زیرا فاز بینابینی مقاومت الکتریکی تماسی بیشتری نسبت به فولاد و بتن دارد. بنابرین مقاومت الکتریکی تماسی نشانه خوبی از گسترش خوردگی نسبت به زمان خوردگی میباشد. ارتباط بین استحکام پیوند و مقاومت الکتریکی تماسی، ارتباط بین قدرت پیوند و پیشرفت خوردگی را نشان میدهد.
در مدت زمان خوردگی مشابه، نمونههای مختلف میتوانند قدرت پیوند و مقاومت الکتریکی تماسی مختلفی را داشته باشند. زیرا نمونههای مختلف درجه تمیزی سطح مختلف، حتی پیش از خوردگی را دارند. مسئله پراکندگی دادهها میتواند با استفاده از اندازهگیری استحکام پیوند و مقاومت الکتریکی تماسی برای هر نمونه و بررسی ارتباط بین این دو کمیت در نمونههای مختلف در مدت زمان خوردگی مشابه، جبران شود. منحنی که این ارتباط را توجیه میکند، با افزایش مدت زمان خوردگی شیفت پیدا میکند. بنابرین تأثیر خوردگی بر استحکام پیوند به راحتی با وجود پراکندگی دادهها قابل اندازهگیری خواهد شد. روش اندازهگیری مقاومت الکتریکی تماسی و استحکام پیوند برای هر نمونه تست الکترومکانیکال نام دارد.
شکل ۱ و ۲ منحنیهای مقاومت الکتریکی تماسی در مقابل استحکام پیوند را در مدت زمان ۱ الی ۹ هفته خوردگی نشان میدهد. استحکام پیوند با افزایش مدت زمان خوردگی در مدت ۱ الی ۵ هفته افزایش یافته، افزایش مشابه نیز از ۱ تا ۳ هفته در شکل ۱ نشان داده شده است. در هر حال استحکام پیوند با افزایش مدت زمان خوردگی از ۵ الی ۹ هفته کاهش پیدا میکند، و کاهش مشابه از ۵ تا ۷ هفته در شکل ۲ نیز دیده میشود. مقاومت تماسی با افزایش مدت زمان خوردگی از ۱ الی ۵ هفته افزایش پیدا میکند (شکل ۱). و همچنین از ۴ تا ۹ هفته نیز افزایش پیدا میکند (شکل ۱ و ۲).
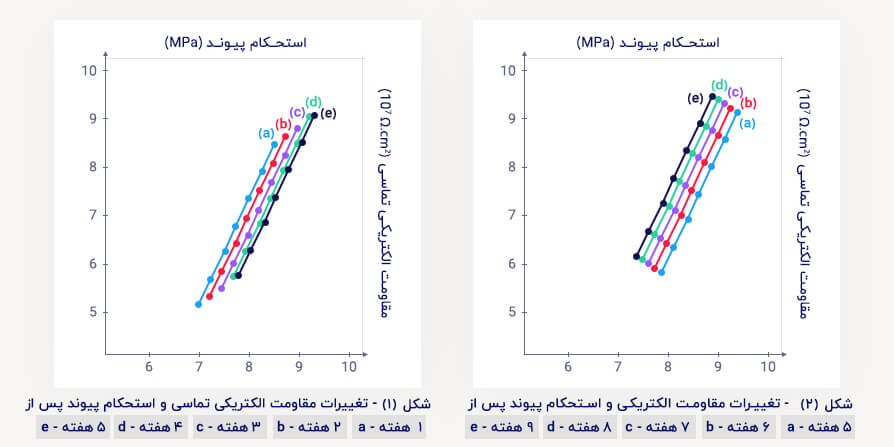
شکل ۳ و ۴ استحکام پیوند (مقدار میانگین برای هر نمونه در هر مدت زمان خوردگی معین) و مقاومت تماسی (مقدار میانگین برای هر نمونه در مدت زمان خوردگی معین) را به ترتیب در طول ۹ هفته اول خوردگی نشان می دهد. هم استحکام پیوند و هم مقاومت تماسی در طول ۵ هفته خوردگی افزایش پیدا کرده است. در بیش از ۵ هفته خوردگی استحکام پیوند با پیشروی خوردگی کاهش می یابد. و مقاومت تماسی همچنان افزایش می یابد. این بدان معنی است که استحکام پیوند تا یک حدی که فولاد دچار خوردگی می شود افزایش می یابد ولیکن با افزایش بیشتر فاز خوردگی استحکام پیوند کاهش می یابد. این نتیجه با این یافته سازگار است که غوطه وری میلگرد فولادی در آب قبل از اختلاط در بتن باعث افزایش استحکام پیوند می شود ، اما زمان غوطه وری بیش از حد (بیش از ۵ روز) باعث می شود مقاومت پیوند از مقدار بالایی که پس از غوطه وری به مدت ۲ تا ۵ روز به دست می آید ، کاهش یابد. شکل ۴ نیز این حقیقت راثابت می کند که مقاومت تماسی بطور با قاعده با افزایش زمان خوردگی و همچنین غوطهوری در آب افزایش پیدا میکند. همچنین شکل ۴ نشان میدهد که مقاومت تماسی در مرحله های ابتدایی خوردگی نسبت به مراحل بعدی خوردگی به صورت شارپتر افزایش پیدا میکند. زیرا انتقال الکترون به دلیل وجود فاز بینابینی (فاز اکسیدی) محدودتر میشود.
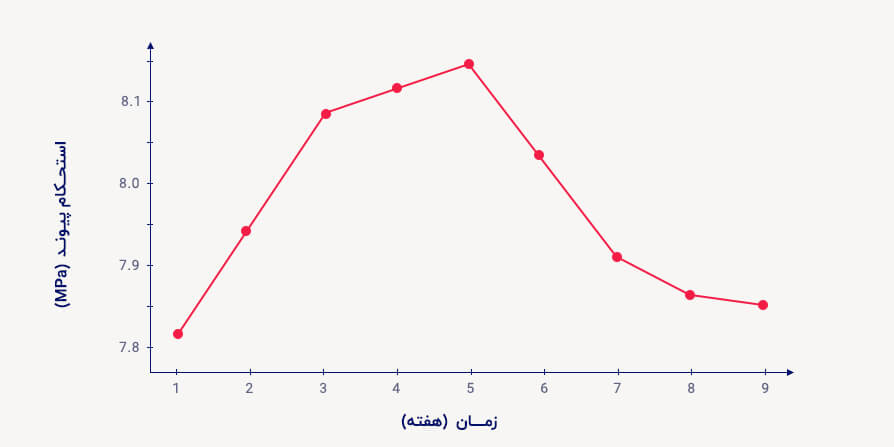
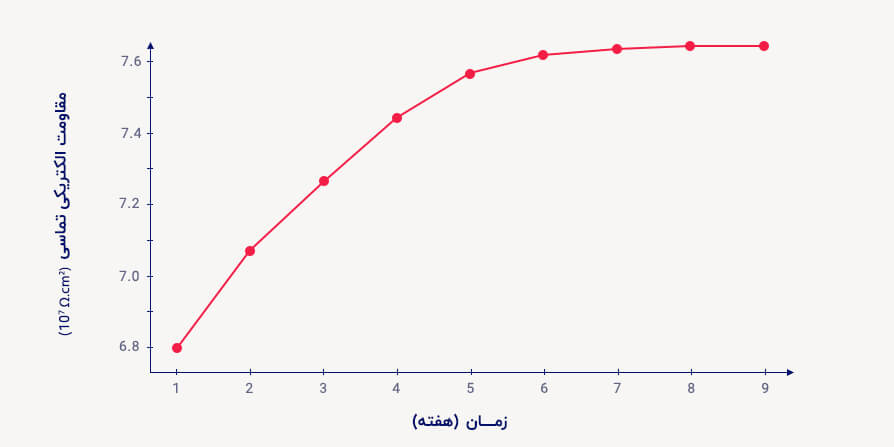
نتیجه گیری
یکی از مهمترین عوامل تخریب سازههای بتن آرمه به ویژه در مناطق مرطوب خوردگی میلگرد میباشد. خوردگی میلگرد سبب ایجاد ترک در پوشش بتنی میلگرد شده و در نهایت تخریب سازه بتنی را به همراه دارد. بنابرین پیشگیری از خوردگی فولاد و کنترل میزان رطوبت موجود در ساختار بتن از اهمیت خاصی برخوردار است. طبق بررسیهای انجام شده درنتیجه خوردگی فولاد و ایجاد فاز بینابین (فاز اکسیدی) در ابتدا استحکام پیوند میلگرد فولادی و بتن افزایش یافته و سپس کاهش مییابد. این حقیقت دال بر این موضوع میباشد که میزان رطوبت موجود در بتن میبایست در حد کنترل شده باشد که طبق بررسیهای صورت گرفته این مقدار حدودأ ۶۰ درصد وزنی ساختار بتن میباشد.